Asian Petrochemicals is experiencing rapid and fundamental changes: China is becoming Asia's largest petrochemical producer; Middle East production capacity is increasing based on cheap natural gas; With the growth of economy, the demand for basic chemicals in China has great potential; Discovery of India's KG-D6 gas field It will increase the space for petrochemical production naphtha and export naphtha in the region.
Asian ethylene production capacity is rapidly increasing. By the end of 2009, Asia’s ethylene capacity will be approximately 43.8 million tons/year, and by the end of 2015 production capacity will increase by 16 million tons/year. In the second half of 2009 alone, the region increased its ethylene capacity by 4.1 million tons/year, and Fijian Global Energy expects ethylene capacity in Asia to increase by 5.4 million tons/year in 2010.
About 50% of new ethylene capacity from 2009 to the end of 2015 occurred in the second half of 2009 and 2010, and it is mainly in China and India. China will account for 54% of new production capacity in 2010-2015. At present, China's ethylene production capacity lags behind the United States at a rate of 25 million tons/year, ranking second in the world, and the gap with the United States is rapidly narrowing.
At the end of 2009, China’s ethylene production capacity was 13.9 million tons/year, and it will increase by 8.7 million tons/year by 2015, of which 42% of new production capacity will be put into production in the next two years. By 2015, China's ethylene production capacity will exceed the sum of Japan, South Korea, and Taiwan.
Compression injection molding: it is an advanced form of traditional injection molding.Advantages: it can increase the flow length ratio of injection molded parts; Adopt less clamping force and injection pressure; Reduce the internal stress of materials; And improve processing productivity.Injection compression molding is applicable to products made of various thermoplastic engineering plastics, such as large-size curved parts, thin-walled parts, miniaturized parts, optical lenses, and parts with good impact resistance requirements.
Low pressure injection molding:Low pressure injection molding process is a packaging process that uses very
low injection pressure to inject hot-melt materials into the mold and solidify rapidly. With the excellent sealing performance and excellent physical and chemical properties of hot-melt materials, it can achieve the effects of insulation, temperature resistance, impact resistance, vibration damping, moisture-proof, waterproof, dustproof and chemical corrosion resistance, and play a good role in protecting electronic components.
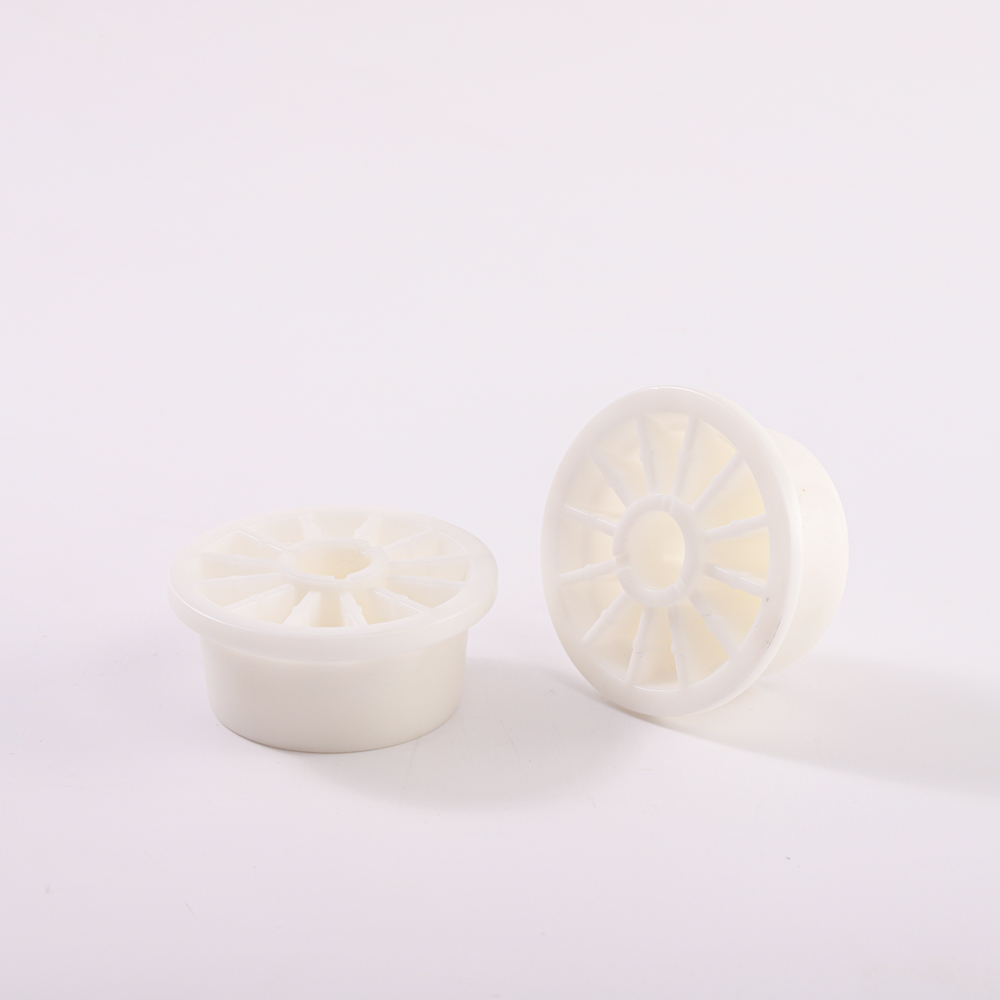
Plastic Parts Design Services,Double Color Plastic Injection Molding Design,Custom Injection Molding Services,Custom-Built Plastic Parts Design Services
Suzhou Dongye Precision Molding Co.,Ltd. , https://www.sjinjectionmolding.com